What is continuous improvement?
- Guides
- Innovation & Continuous Improvement
- What is continuous improvement?
Think of continuous improvement as the ongoing quest to do things better - to improve quality, to increase efficiency, and to reduce costs. Improvements can be done as small incremental improvements over time, or as breakthrough improvements all at once.
Continuous improvement vs. innovation
Although innovation and continuous improvement seem very similar, they are unique concepts. If you remember back to our definition of innovation - fresh thinking that creates value - continuous improvement doesn't always require fresh thinking.
For example, if you have an inefficient process and you rearrange the steps or eliminate a step, that's not innovation. You may have improved the process, but you've not done anything new or creative.
However, if you created a new tool to make the process more efficient, or re-structured the process in a way that no-one had seen before, that is both innovation and continuous improvement.
Continuous improvement models
Continuous improvement models are structured methodologies for implementing continuous improvement. There are three main models to look at:
- Lean (this is the primary focus of this module)
- Six Sigma
- Lean Six Sigma
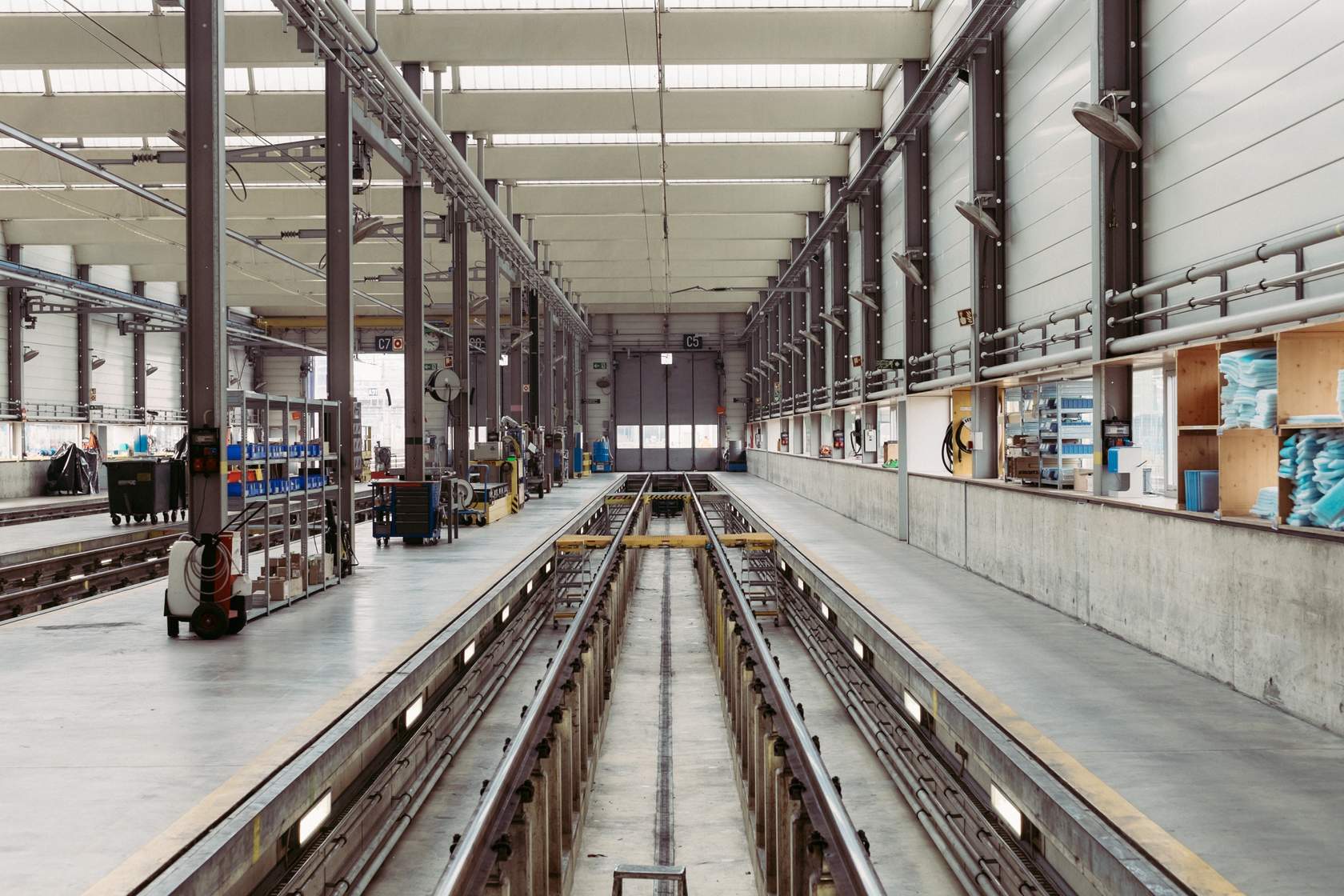
1. Lean
Lean is a continuous improvement model based on the Toyota production system, which focuses on the elimination of waste - waste being any additional time, labour or materials used in the production of goods and services that doesn't add value to the process. Through the reduction or elimination of waste, Lean helps an organisation keep costs down and achieve the maximum output for every input.
Also, with less waste in the production and delivery process, customers receive their orders faster, which leads to improved customer satisfaction.
Although Lean started as a concept to improve efficiency in the manufacturing process, the principles of waste reduction can be applied to virtually any industry.
The 7 wastes
Processes are analysed across 7 different areas to identify potential waste.
- Defects - defect waste is generated when there are issues with products that the customer would deem unacceptable. This requires re-work to fix the defect or requires the product to be rejected entirely.
- Inventory - inventory waste is generated whenever raw materials, work-in-progress (WIP), or finished goods that are not directly required to fulfil current customer orders are being handled or taking up space.
- Motion - motion waste is generated whenever you move people around unnecessarily. Motion can best be described by this quote: “To move and add value is called work. To move and not add value is called motion."
- Over-processing - processing waste is generated when something is handled, worked on, or otherwise dealt with more than is necessary.
- Over-production - production waste is generated when products are produced surplus to demand. Over-production is particularly undesirable because it leads to waste in all of the other 6 areas.
- Transportation - transport waste is generated whenever objects are moved around unnecessarily. During transportation no value-adding activities can be performed. With additional handling there is also a risk of damage.
- Waiting - waiting waste is generated when people, parts, systems or facilities are waiting for something before they can start being productive and creating value.
The Lean process (Plan, Do, Check, Act)
To improve processes and eliminate identified waste, the Lean process uses the PDCA cycle (Plan, Do, Check, Act). This is also commonly known as the Deming Cycle after W. Edwards Deming, who introduced the concept in Japan in the 1950s. The PDCA cycle is an improvement cycle based on the scientific method of proposing a change in a process, implementing the change, measuring the results, and taking appropriate action.
The four stages of the PDCA cycle are:
- Plan - Define the problem, determine the goals for a process and the needed changes to achieve them.
- Do - Test/implement the changes.
- Check - Evaluate the results.
- Act - If changes are needed, repeat the cycle. If not, standardise the new approach.
There is also a variation of this model that includes an additional step, Observe, which comes before the planning stage. We will explore this model in more detail in the next section.
2. Six Sigma
Six Sigma is a quality management methodology that was pioneered by Motorola in the 1980s. It was originally developed to improve the manufacturing process to near perfection (only 4 defects for every 1 million units produced), but has since been applied across a host of industries outside of manufacturing. Where Six Sigma can be achieved, defects or errors are virtually eliminated, which reduces wastage and unnecessary cost.
People involved in Six Sigma go through a rigorous training program that leads to the gaining of coloured belts up to a black belt, much like in martial arts.
The DMAIC Framework
Six Sigma uses the DMAIC (Define, Measure, Analyse, Improve, Control) framework to manage the improvement process.
- Define - define the goals of the improvement activity.
- Measure - measure the current state (i.e. how things are now).
- Analyse - analyse the data and identify ways to bridge the gap between the current state and the end goal.
- Improve - implement the improvements.
- Control - put control measures in place to guard against performance regressing and transfer control of the process from the project team to the process owner.
3. Lean Six Sigma
Many organisations use a hybrid Lean Six Sigma approach, which gives them the flexibility to choose from the best tools from Lean and the best tools from Six Sigma, and use whichever is most suitable for the particular problem.Learn more
Next: Innovation & Continuous Improvement - Using the OPDCA cycle